X10CrNi18-8, 1.4310, 301, 301S21, Z12CN17-07 Stainless Steels to EN 10088-1
X10CrNi18-8, 1.4310, 301, 301S21, Z12CN17-07 - Specification & Application
- EN 10088-1 - Stainless steels - Part 1: List of stainless steels
- EN 10088-2 - Stainless steels - Part 2: Technical delivery conditions for sheet/plate and strip of corrosion resisting steels for general purposes
- EN 10088-3 - Stainless steels - Part 3: Technical delivery conditions for semi-finished products, bars, rods, wire, sections and bright products of corrosion resisting steels for general purposes
- EN 10151 - Stainless steel strip for springs - Technical delivery conditions
- EN 10263-5 - Steel rod, bars and steel wire for cold heading and cold extrusion - Part 5: Technical delivery conditions for stainless steels
- EN 10264-4 (2002) - Steel wire and wire products - Steel wire for ropes - Part 4: Stainless steel wire
- EN 10270-3 - Steel wire for mechanical springs - Part 3: Stainless spring steel wire
- DIN 17440 - Chromium-nickel austenitic stainless steel
Steel wire for mechanical springs - Part 3: Stainless spring steel wire
Chemical composition(wt.%) of X10CrNi18-8, 1.4310, 301, 301S21, Z12CN17-07 grade: to EN 10088-1
Elements |
Min.(≥) |
Max.(≤) |
Similar |
Remarks |
C |
0.05 |
0.15 |
|
|
Si |
- |
2.00 |
|
|
Mn |
- |
2.00 |
|
|
P |
- |
0.045 |
|
|
S |
- |
0.015 |
|
|
Cr |
16.00 |
19.00 |
|
|
Mo |
- |
0.08 |
|
|
Ni |
6.00 |
9.50 |
|
|
N |
- |
0.11 |
|
|
Mechanical properties of grade X10CrNi18-8, 1.4310, 301, 301S21, Z12CN17-07 grade: to EN 10088-1
Yield Strength,Rp 0.2(MPa)
Condition |
Min |
Max |
Similar |
Note |
|
195 |
|
400 N/mm2 |
|
Tensile Strength,Rm(MPa)
Condition |
Min |
Max |
Similar |
Note |
|
500-750 |
|
710 N/mm2 |
|
Impact,Kv/Ku(J)
Condition |
Min |
Max |
Similar |
Note |
Elongation,A(%)
Condition |
Min |
Max |
Similar |
Note |
|
45 |
|
|
|
Reduction of area,(%)
Condition |
Min |
Max |
Similar |
Note |
Hardness
Condition |
Type |
Min |
Max |
Similar |
Note |
|
HB |
|
230 |
|
|
Physical properties of grade X10CrNi18-8, 1.4310, 301, 301S21, Z12CN17-07 EN 10088-1
Density(kg/dm3) |
Note |
7.9 |
|
Electrical resistivity at 20°C (Ω mm2/m) |
Note |
0.73 |
|
Magnetizability |
Note |
slight |
|
Thermal conductivity at 20°C (W/m K) |
Note |
15 |
|
Specific heat capacity at 20 °C (J/kg K) |
Note |
500 |
|
Thermal expansion (K-1) |
Note |
20 – 100 °C: 16.0 x 10-6 |
|
X10CrNi18-8, 1.4310, 301, 301S21, Z12CN17-07 - Detail
1.4310 is essentially a leaner version of 1.4301, which as a result of its combination of high
chromium and restricted nickel content, produces a metastable austenitic structure which will
work harden / strengthen very rapidly when subjected to cold deformation. Since this steel is
used for the production of spring components, the final microstructure will contain a significant
amount of shear induced martensite and as such will be relatively magnetic.
Heat treatment and mechanical properties
Optimal material properties are realised after solution annealing in the temperature range 1000 °C – 1100 °C followed by rapid cooling in air or water. Since this grade of steel is susceptible to precipitation of chromium carbides, care must be taken to limit the time spent in the temperature range 450 °C to 850 °C, both during fabrication and service. In the solution annealed condition, the following mechanical properties may be attained when testing in the longitudinal direction:
Applications
Automotive industry,Various corrosion resisting spring components,chemical industry,food and beverage industry,electronic equipment
Elevated
temperature
properties
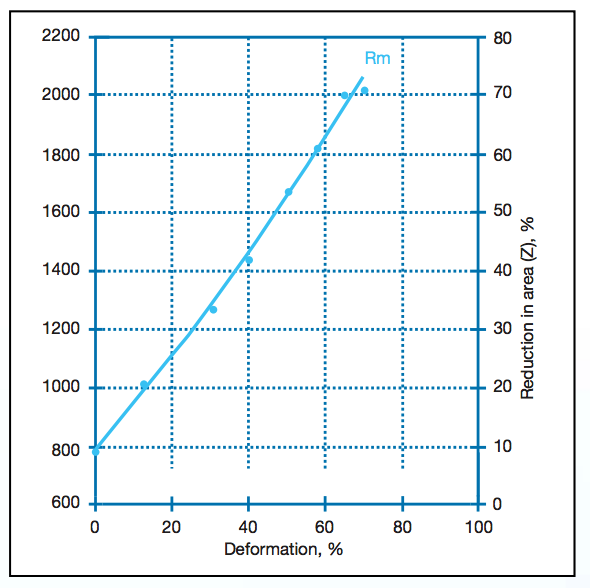
Welding
Since 1.4310 is primarily used for the production of springs, there is generally no requirement
for welding. Should welding be required, however, 1.4310 is weldable with or without the use
of filler material. If the use of a filler metal is required, then the use of Novonit 4316 (AISI 308L)
would be recommended. A maximum interpass temperature of 200 °C must be adhered to.
Post weld heat treatment is not necessary. Please note that welding of cold worked components
will result in the welded zone displaying significantly reduced mechanical properties compared
with the rest of the weldment.
Forging
1.4310 is usually heated to within the range 1150 °C – 1180 °C to allow forging to take place
at temperatures between 1200 °C and 900 °C. Forging is followed by air cooling, or water
quenching when no danger of distortion exists.
Machining
The combination of low thermal conductivity and extremely high work hardening rate serves to
make 1.4310 difficult to machine. The following cutting parameters are thus proposed as a
guideline when machining NIRO-CUT® 4310 using adequate cooling and coated hard metal
cutting tools.

Product shapes we supply:
- Tool Die Steels in the X10CrNi18-8, 1.4310, 301, 301S21, Z12CN17-07 Stainless Steels grade
- Stainless Steels - Special Steels in the X10CrNi18-8, 1.4310, 301, 301S21, Z12CN17-07 Stainless Steels grade
- Square and Flat Steel in the X10CrNi18-8, 1.4310, 301, 301S21, Z12CN17-07 Stainless Steels grade
- Coil Sheet in the X10CrNi18-8, 1.4310, 301, 301S21, Z12CN17-07 Stainless Steels grade
- Bar and Hollow Bar in the X10CrNi18-8, 1.4310, 301, 301S21, Z12CN17-07 Stainless Steels grade
- Forgings in the X10CrNi18-8, 1.4310, 301, 301S21, Z12CN17-07 Stainless Steels grade
- Superalloy in the X10CrNi18-8, 1.4310, 301, 301S21, Z12CN17-07 Stainless Steels grade
- Tube Pipe in the X10CrNi18-8, 1.4310, 301, 301S21, Z12CN17-07 Stainless Steels grade
- Non-Magnetic Steel in the X10CrNi18-8, 1.4310, 301, 301S21, Z12CN17-07 Stainless Steels grade
- Steels of Blade for Steam Turbine in the X10CrNi18-8, 1.4310, 301, 301S21, Z12CN17-07 Stainless Steels grade